In the Maintenance Repair Overhaul (MRO) field, efficient, high-quality production comes down to teamwork and dedication. We are fortunate to work with a team with a relentless commitment to keep the promises we make to every one of our customers who entrust us with their extremely valuable and time-sensitive hardware.
We leverage that drive and commitment in a multi-pronged effort to meet the customer’s requirements in Quality, Engineering, and Production. Dive into our collaborative quality efforts below.
Behind the Walbar Peabody Ethos
It’s no secret to anyone in the industry that the MRO business is rife with challenges, given the life duty and various service performances these engines provide.
The Vacuum Furnace Braze Repair and Furnace Coatings Application processes are a case in point. Over the years, we’ve worked tirelessly with our customers and pooled resources from our Management, Engineering, and Quality teams to overcome these challenges and solve problems. We’ve developed proprietary braze techniques and coating mixtures that have been tried and tested in compliance with a repair process designed specifically to fit our customers’ various product lines.
The above, combined with an emphasis on the Continuous Improvement efforts to streamline our “Work In Progress” (WIP) flow management program, gives our customers a significant advantage by choosing Walbar Peabody. This is the heartbeat of our company: Our highly skilled and passionate team with decades of experience and desire to meet the needs of our customers, which fuels the dedication and commitment to innovate.
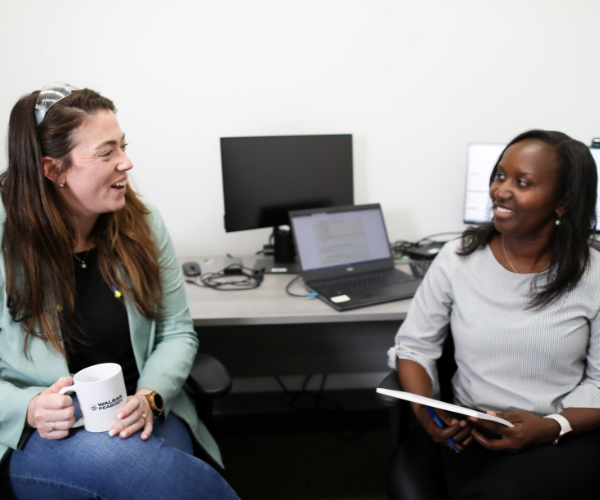
A Multi-Collaborative Effort
The term “multi-collaborative effort” might better describe our production process.
For us, however, the MRO business is vastly different from the Original Equipment Manufacturer (OEM) business. The approach to dealing with repair needs requires a significant degree of support from these three entities:
- Engineering: Find compliant solutions to various repair challenges that may be beyond current capability.
- Quality: Review proposed solutions to ensure compliance and proper documentation per the FAA and manufacturer.
- Production: Implement and execute these solutions according to our customers’ cost and time requirements.
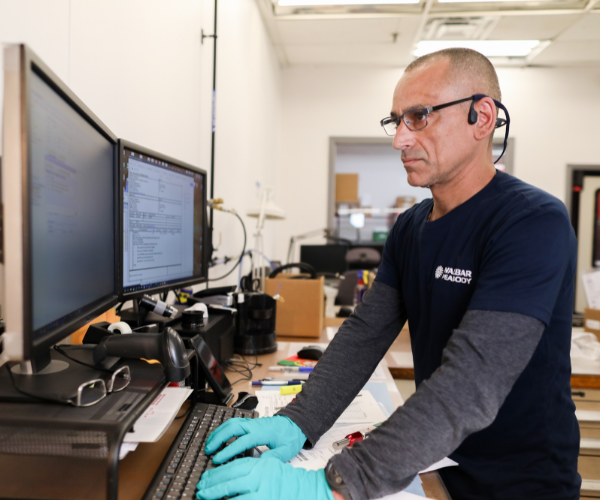
Our Work In Process/Progress (WIP)
When a customer’s hardware arrives, it undergoes our substantiated repair process. Sometimes, the damaged hardware may be in a condition that requires collaboration to continue.
This assessment will prompt the decision to scrap or repair the component(s). Once we’ve decided to repair, the hardware begins its journey through our WIP process.
At this point, the hardware is in the hands of Production to manage that journey, which entails:
- Streamlining the process by cross-training team members through multiple disciplines to keep Queue time to a minimum at every operation along the way
- Quickly assessing in-process issues due to various degrees of repair needed
- Very close attention to our promised due date
Our process calls for a Continuous Improvement assessment effort as we constantly aim to elevate quality and efficiency.
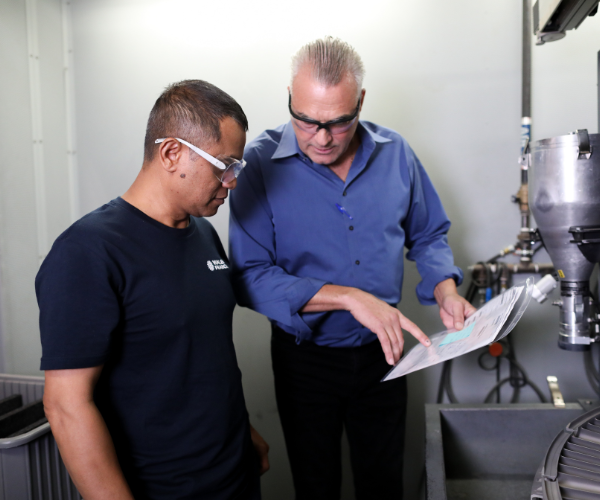
Striving for Better with Every Customer
At the end of the day, turn-around time (TAT) and on-time delivery (OTD) are the daily, weekly, and monthly goals for production. Because of our WIP management program, we achieve and hold among the best, if not the best, TAT and OTD rates in the industry for these product lines.
Are you ready to learn how Walbar Peabody will exceed your quality and time expectations? Contact us today to chat about getting your aircraft off the ground.