Quality and safety go hand-in-hand, especially in the aerospace industry. This is why quality control is at the center of everything we do here at Walbar Peabody.
To maintain the high standard of quality that Walbar Peabody has become known for, our Quality Control Team collaborates daily with the Customer Experience, Production, and Engineering Teams to drive improvement, innovation, and collaboration at the facility. Our mantra is “Just because something has always been done one way, does not mean that it cannot be improved upon, made safer, or made more mistake-proof.” At Walbar Peabody, quality does not belong to one entity. It is the responsibility of everyone, from induction of a part to its final shipment.
Of course, some challenges require unique solutions. Keep reading for a behind-the-scenes look at our Quality Control Team’s role and how they ensure Walbar Peabody’s reputation for first-time quality endures.
Quality Control Challenges & Solutions
Walbar Peabody has a new group of Quality Team members who are eager to build upon the solid reputation that customers have come to expect from Walbar Peabody. The team is constantly discovering ways in which tried-and-true processes can be further standardized and centralized, thus providing easier access for our technicians and smoother workflow on the shop floor.
A recent example of this involves the creation of a “one-stop-shop” database that our Inspection Team will use to complete Block 12 of FAA Form 8130. This database, maintained by the Engineering Team, lists the latest revisions to engine manuals, service bulletins, etc., and allows the inspectors to focus on just that, inspecting, rather than searching through customer websites for the latest revisions of technical documents.
We’re also moving into the digital age by using scanners to store all records and technical information, using tablets on the shop floor to have access to the latest revisions of work instructions, and utilizing SharePoint to manage items in our Quality Clinic.
Consistent refinement of our processes and procedures is necessary when dealing with new updates, revisions, and part numbers. The goal is to make everything we do as mistake-proof as possible, which ultimately saves customers time and money.
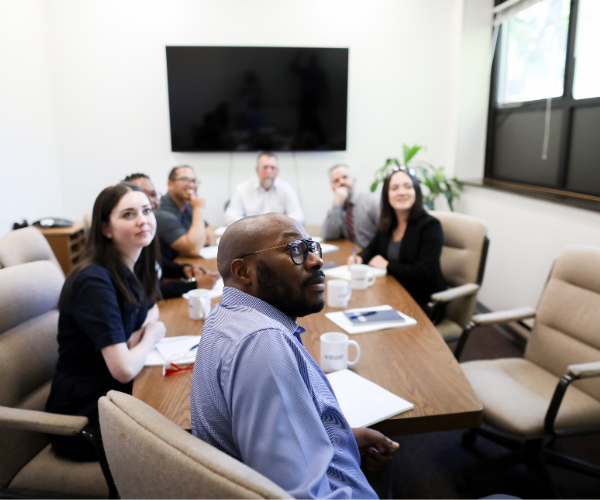
What Sets Our Quality Control Apart?
Walbar Peabody is fortunate to have a great team of people who love their jobs and take great pride in their work. Nearly everyone on the Production Team has been with Walbar Peabody for 20+ years and is an expert at what they do. So, although we are a smaller operation, our customers can rest assured knowing that they have one of the most experienced people on earth working on their parts. To build upon that expertise and further the mission of first-time-quality, the Production, Engineering, and Quality Teams are constantly working together to innovate, standardize, and centralize.
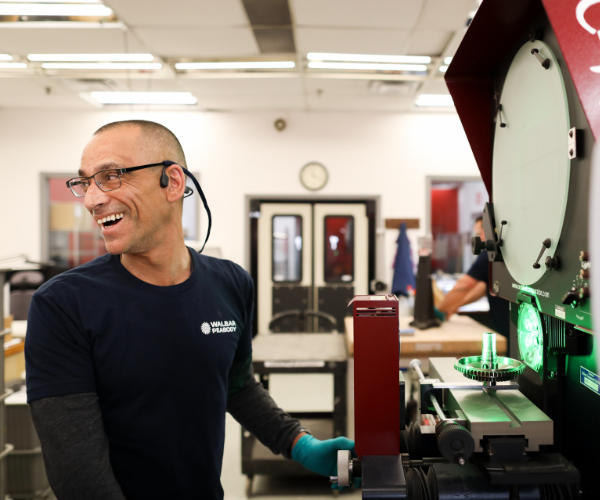
Maximum Quality Means Maximum Safety
In the world of jet engines and their many components, quality control is non-negotiable—after all, our work directly impacts the safety of anyone who flies on an airplane, including us! There is absolutely no room for cutting corners in our line of work. Hence, safety is paramount!
With safety and quality at the forefront of our minds, we make it a priority to practice transparency with our customers and fellow team members. From leadership on down, we trust each colleague to work and act with integrity. If this means pausing production efforts to work out a potential problem, that is what we’ll do to ensure the highest quality and safety standards are maintained.
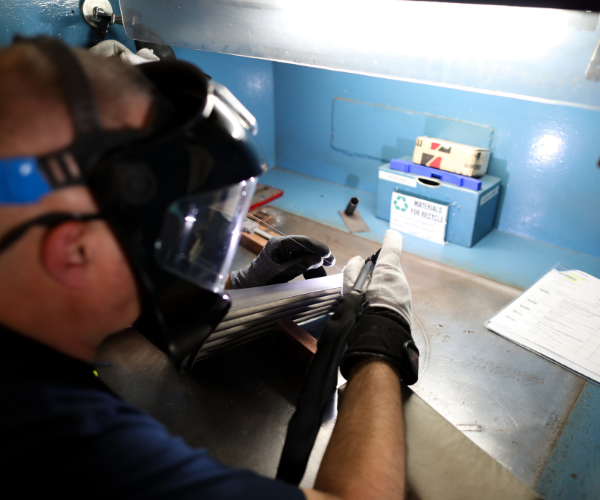
If this level of passion for safety, integrity, and quality is what your company is looking for in a maintenance repair overhaul partner, contact Walbar Peabody today! Our customer experience team is ready to answer your questions and guide the way to a successful partnership!