In the aviation industry, quality and safety go hand-in-hand—which is why quality is our top priority in every aspect of what we do here at Walbar Peabody. So, it’s no surprise that we undergo dozens of internal and external audits from both third-party organizations and clients to review processes and documentation.
For example, our site is AS9100 certified, so third-party auditors audit and recertify us. We also conduct around 30 internal audits per year, in addition to NADCAP audits for our specialized processes.
Quality is up to everyone at Walbar Peabody, so our teams collaborate cross-functionally. Learn more about why these various audits are essential to our continual improvement.
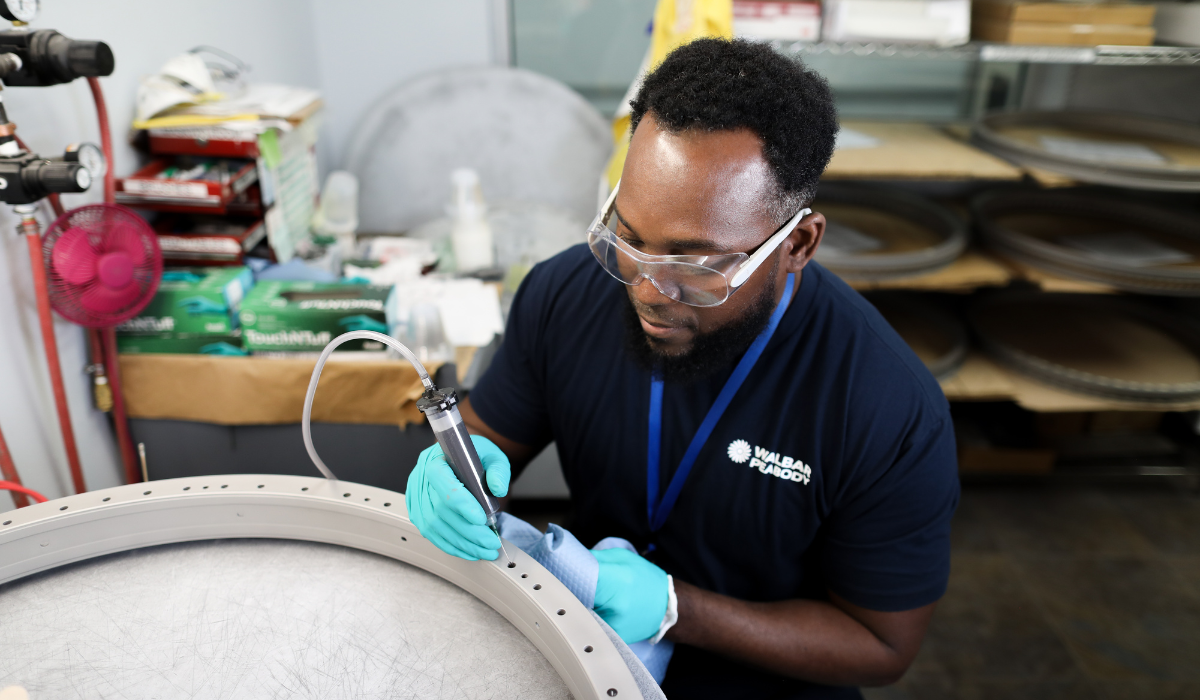
How Audits Fuel Process Improvement
We prepare for every audit to minimize findings. We find that the pre-audits result in many practice and documentation improvements during the audits. After the audits, we review our findings and work to resolve them quickly through robust corrective action.
Walbar Peabody is a relatively small site—despite our high output! This level of productivity entails effort from not only the engineering and quality teams but also the customer service, business development, and sales production departments. Every employee does their part and is very willing to work together to make sure we overcome any audit findings.
As a small, close-knit team, our employees’ input regarding crucial areas like quality control has a more significant impact. They understand that every facet of their work matters. Plus, they get to both make these positive changes and then see them in action as issues are resolved, easing processes for their fellow team members.
All of the above creates a culture of safety and top-notch quality.
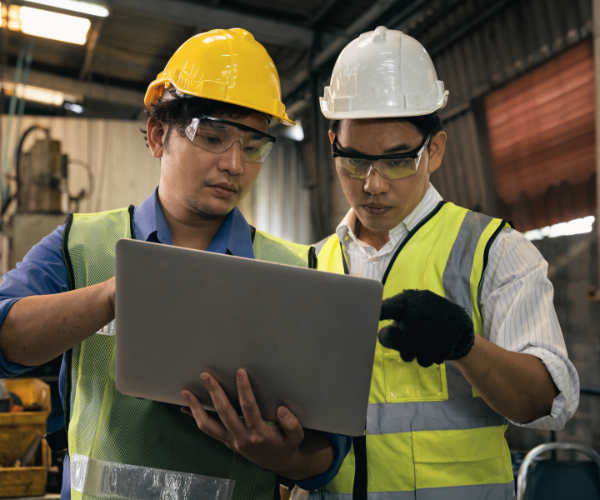
A Closer Look at Quality Audits
Internal audits tend to be very site-specific. Our quality control team performs audits of anything from reviewing documentation of one department to talking with employees to see if what they’re doing on the floor matches our documentation.
Specific third-party organizations are authorized to audit and certify us for external audits for annual recertifications like AS9100, NADCAP, and EASA. For instance, NADCAP is very specific and entails specialty processes, so a NADCAP auditor will come in and evaluate these processes to ensure we’re meeting their specs and requirements.
Finally, we are subject to audits from clients like Pratt & Whitney Canada and GE because we work on many of their parts. We work with our customers to ensure our product complies with their standards. Since much of our work is in maintenance repair overhaul (MRO), many of our processes are frozen—meaning they can’t change without permission from the customer. So, the customer will come onsite to ensure we’re still following these processes and their latest documentation.
Quality & Safety First
…which is why audits are vital! And since our philosophy at Walbar Peabody is that every employee is involved in quality control, we all take equal pride in constant improvement and delivering the best service and products for our customers.
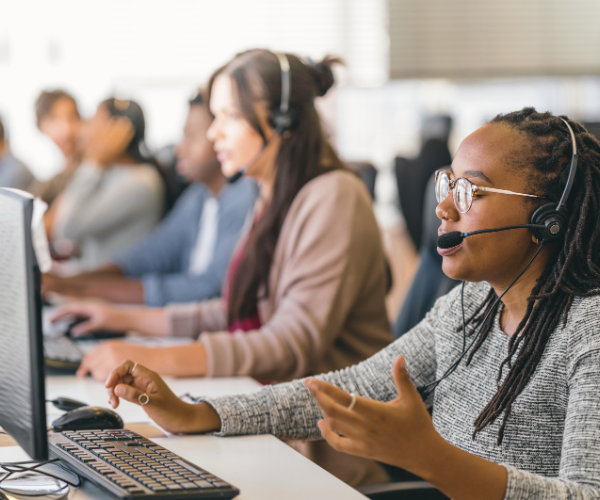
Are you seeking an MRO partner to minimize your aircraft’s downtime and maintain safe, efficient service? Contact us today to learn more about how we can help.